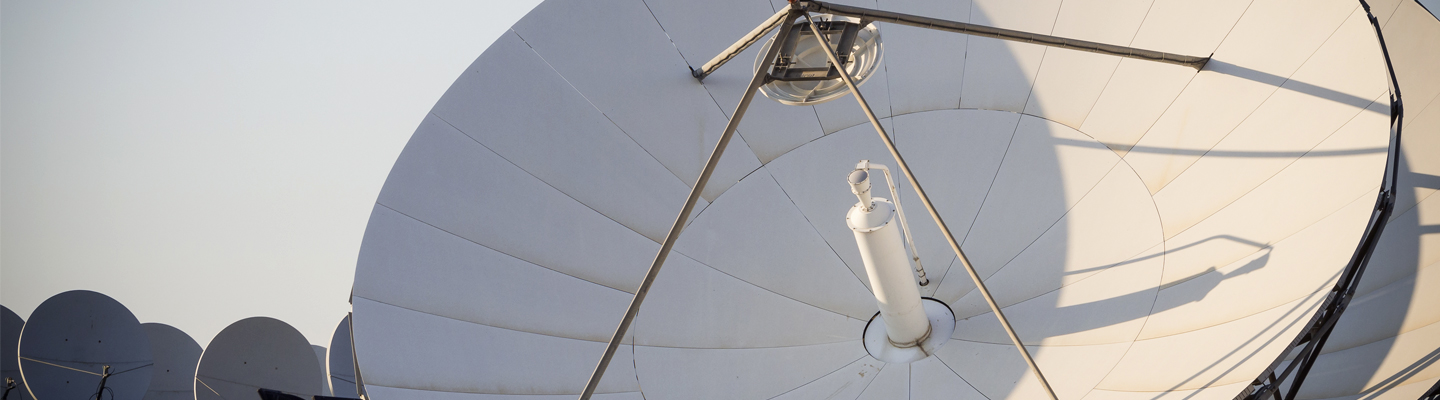
Telecommunications
Telecommunications
We’ve moved from “can you hear me now” to being able to access just about anything from your phone. Improvements in bandwidth and mobile architecture designs keep changing the game. The greater power density of 5G has produced increased levels of heat, yet towers and devices are exposed to harsh weather conditions 24/7.
Novagard’s electronics grade silicone adhesives and sealants protect sensitive components in some of the harshest conditions on earth. They not only resist 5G’s higher temperatures, their low modulus means they also relieve a superior amount of stress when materials expand. Their high insulation resistance results in excellent EMI shielding. And their superior hydrolytic stability is especially important in protecting towers, base stations, and transmitters from high humidity, rain, or snow.
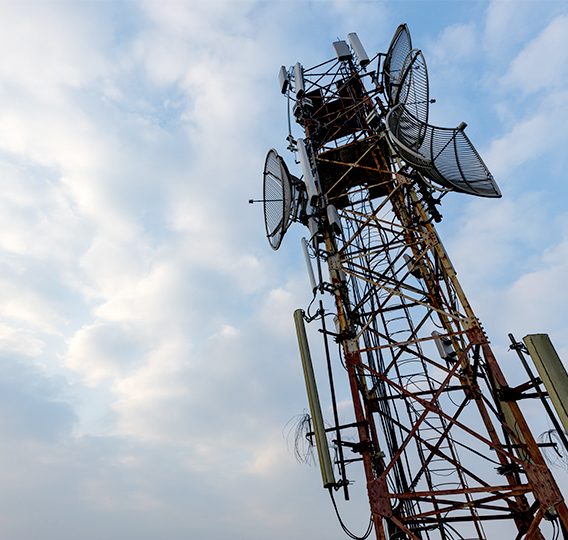
Advantages to selecting a silicone cured with UV light:
- 3 – 5 second cure
- Total cost of ownership is lowered
- No work in process/can immediately move to the next manufacturing step
- High-energy ovens are replaced with low-energy UV LED options
- Low capital equipment footprint
- Sustainable
- Convenient, single component format
- Very little to no shrinkage
- Dual cure options to cure shadow areas
-
Electronics Grade (Alkoxy) Silicones
500-210 is a balanced-performance clear sprayable silicone coating featuring a room temperature alkoxy moisture cure that can be accelerated with heat. This silicone is UL 746E certified and has a V-1 rating for flammability.
500-228 cures to a tough, strong, resilient gel to provide protection from both physical damage and mechanical stress and strain relief in addition to great dielectric properties.
500-09x is a high performance UL-rated electronics adhesive. This one-part UL flame rated paste is for applications that require superior bond strength and flame resistance.
-
UV Cure and UV/Dual Cure Silicones
800-401 is a UV-only, fast-curing paste with adhesion to many plastics. With nominal viscosity of 300,000 cPs, 800-401 consistently holds its shape even when dispensed into complex shapes.
800-754 is a UV-cure only pottant that cures to a soft, compliant elastomer that relieves stress and strain on delicate components. 800-754 will UV-cure to a depth of 14mm in a single pass.
800-755 is an incredibly soft non-corrosive, single-component gel and is an ideal pottant or encapsulant that will also dramatically increase your throughput.
800-260 is a first-generation conformal coating for printed circuit boards. While its oxime secondary moisture cure provides improved physical properties, it offers limited adhesion and can present potential corrosion issues in enclosed applications. This silicone is rated UL 746 E and V-1.
With viscosity of 50,000 cPs, 800-750 clings readily to components for staking and glob-top applications.
800-230 is a UV curable self-leveling silicone pottant that offers a higher viscosity coating option, while still remaining flowable.
800-235 is UV-cured, semi-flowable material. A UV-cure only silicone with limited adhesion, its higher viscosity makes it ideal for cured-in-place gaskets.
800-400 is a UV-only, fast-curing paste without adhesion. With nominal viscosity of ~300,000 cPs 800-400 consistently holds its shape even when dispensed into complex shapes.
800-610 is a low viscosity, pourable or sprayable encapsulant. Its low viscosity ensures the material flows easily around components for thorough wet-out. This is a UV cure with no secondary moisture cure, offering very low adhesion.
800-520FC is a UV-curable, silicone conformal coating, pottant, or sealant. 800-520FC will cure to a solid elastomer in seconds upon exposure to ultraviolet (UV) light.
800-550 is a UV-curable, silicone coating, pottant, or sealant. With a viscosity of 5,500 cPs, 800-550 flows readily to surround the complex geometry of modern circuitry design.
800-505FC is a UV-curable, silicone conformal coating with a secondary, neutral alkoxy moisture cure for enhanced adhesion and shadow cure. It is UL 746E certified with a V-1 rating for flammability. Utilizing our Fast Cure technology, this secondary moisture cure begins immediately and develops full adhesion in hours.
-
Addition Cure Silicones
600-223 is a platinum catalyzed, addition cure, dielectric potting gel. This is a specialized silicone encapsulant, with low viscosity for easy flowability around complex components.
600-251 is a platinum catalyzed, room temperature, addition cure silicone for potting and encapsulant applications requiring thermal conductivity.
600-250 is a flowable, platinum catalyzed, addition cure, durable encapsulant with good dielectric properties and flame resistance. The high (>90%) transparency of 600-250 allows for easy inspection of components.
-
Industrial Paste Silicones
400-108 is a single-component, moisture-curing silicone paste that cures to a low to medium modulus, rubber-like solid.
400-100 is a single-component, moisture-curing silicone paste that cures to a low to medium modulus, rubber-like solid.
400-102 is one of our single-component, moisture-curing silicone pastes that cures to a low to medium modulus, rubber-like solid.
400-103 is a non-flowable, non-sagging paste product presenting an excellent balance between rate of cure, adhesion, and physical properties.
400-150 is one of our single-component, moisture-curing silicone pastes that cures to a low to medium modulus, rubber-like solid.
400-195 is a non-flowable, non-sagging paste product that provides a fast tack free time and high green strength.
400-196 is a non-flowable, non-sagging paste product that provides a fast tack free time and high green strength.
400-202 is a non-flowable, non-sagging paste product that provides a fast tack free time and high green strength.
400-590 is a smooth, black paste that is ideal for applications that require superior bond strength and moisture resistant sealing in automotive and industrial arenas.
400-110 is a non-flowable, non-sagging paste product that is ideal for industrial applications that require superior bond strength and moisture resistance.
400-118 is a non-flowable, non-sagging paste product that is ideal for industrial applications that require superior bond strength and moisture resistance.
400-155 is a non-flowable, non-sagging paste product that is ideal for industrial applications that require superior bond strength and moisture resistance.
400-900 is a non-flowable, non-sagging low-adhesion paste ideal for creating formed-in- place gaskets where re-entry or post production disassembly is necessary.
400-950 is a non-flowable, non-sagging low-adhesion paste ideal for creating formed-in- place gaskets where re-entry or post production disassembly is necessary.
-
Industrial Flowable Silicones
200-251 is a single-component, oxime-cure silicone for use in applications where the coating needs to flow into small crevices and hard to reach areas.
200-260 is a single-component, oxime-cure silicone for use in applications where the coating needs to be sprayed or to flow into small crevices and hard to reach areas.
200-202 is a single-component, oxime-cure silicone for use in applications where the coating needs to flow into small crevices and hard to reach areas.
Ready-to-use, 200-250 is an oxime-cured silicone used for general industrial sealing and bonding applications requiring a flowable product.
200-102 is a single-component, oxime-cure silicone for use in applications where the coating needs to settle into small crevices and hard to reach areas while maintaining consistency without sagging or running.
200-107 is a single-component, oxime-cure silicone for use in applications where the coating needs to settle into small crevices and hard to reach areas while maintaining consistency without sagging or running.
200-257 is a single-component, oxime-cure silicone for use in applications where the coating needs to settle into small crevices and hard to reach areas while maintaining consistency without sagging or running.
-
NSF Silicone Lubricants
G662 seals and protects electrical connections above and below ground, and is certified to NSF Standard 61 for Drinking Water System Components. G662 can be used as an alternative to Molykote 111 Compound (Dow Corning's DC111).
-
Thermally Conductive Compounds
G641 offers excellent heat transfer in large and small electrical and electronic components and is an ideal material for use in thermocouple wells, power diodes, transistors, semiconductors, and ballasts. G641, or G644 can be used as direct alternatives to Dow Corning / DuPont Molykote DC340.
Versilube G644 is a softer, lower viscosity version of the original Novagard thermal compound, G641. Both G644 and G641 can be used as direct alternatives to Dow Corning / DuPont Molykote DC340.
-
Silicone Greases
G330M is a general-purpose lubricant, offering the highest load carrying capabilities of any Versilube product.
G351 resists oxidation and degradation even under extreme conditions and is formulated to conform with the specifications outlined in MIL-PRF-15719B (formerly MIL-L-15719A). G351 can be used as an alternative for DuPont Molykote 44 (DC44).
G321 has an exceptionally broad operating temperature range; the grease retains its lubricity at temperatures as low as -100°F (-73°C), which makes it well-suited for use in cryogenic systems. G321 is a direct replacement for Dow Corning Molykote 33 Bearing Grease.
G322L is designed for use as a lubricant on aluminum and steel substrates, and contains additives for enhanced corrosion protection.
G326 is designed for a higher load carrying capability, formulated for aluminum and steel substrates.
-
Dielectric Compounds and Lubricants
G623 is specifically formulated for use as a water repellant coating to prevent corrosion, especially in critical applications that require good dielectric properties.
G624 is specifically formulated for use as a water-repellent coating to prevent corrosion and conforms to SAE AMS-8660 (formerly SAEAS-8660 and Mil-S-8660C). G624 is an alternative to DuPont Molykote 4 (DC4).
With lower operating temperature (ranging from -57°C to 200°C), G635 is an excellent dielectric compound with good moisture barrier and corrosion resistance properties. G635 can be used as an alternative to Dow Corning DC 5.
G661 seals and protects electrical connections above and below ground. G661 is most frequently used as a valve and O-ring lubricant, and can be used as an alternative to Molykote 111 Compound (Dow Corning's DC111).
G662 seals and protects electrical connections above and below ground, and is certified to NSF Standard 61 for Drinking Water System Components. G662 can be used as an alternative to Molykote 111 Compound (Dow Corning's DC111).
Designed for use as a dielectric compound on high voltage insulators, G687 reduces the opportunity for dirt and moisture to create arcing across the insulator. It can be used as an alternative to Dow Corning / DuPont Molykote HV3099.
G697 can be used as a lubricant on unpainted ferrous metal surfaces (threaded or unthreaded) to help prevent corrosion, and maintain the condition of the substrate. G697 conforms to MIL-DTL-21567B (formerly MIL-C-21567C).