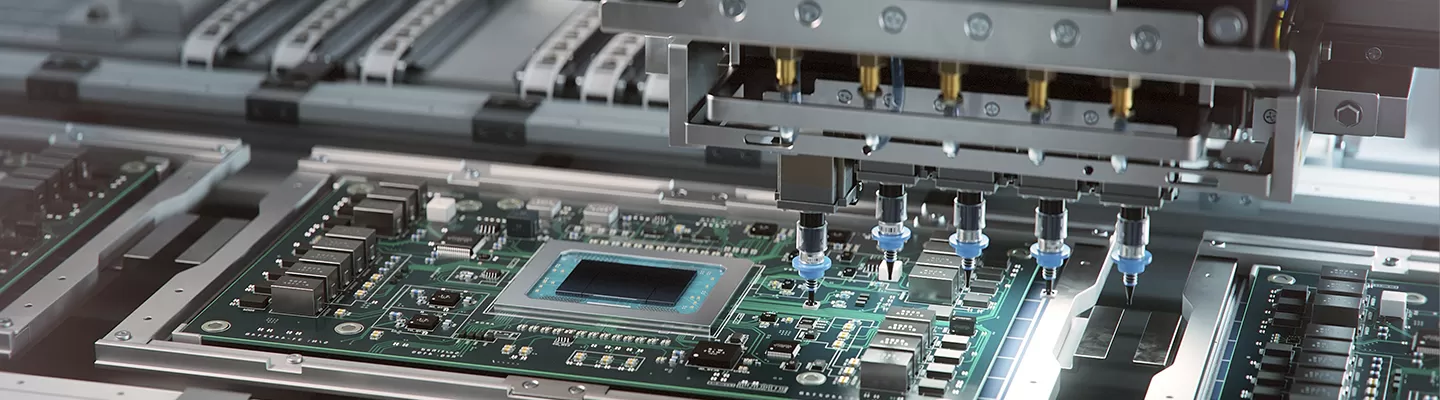
Electronics/PCB Manufacturing
Electronics/PCB Manufacturing
The demands placed on today’s electronics can seem simply overwhelming. Consumers want devices to be smaller and faster. Engineers are requiring more flexibility, power, and durability from components within those devices. Protecting these delicate components demands innovative adhesives and coatings.
Novagard’s electronics grade silicones combine increased flexibility and high temperature resistance, allowing you more versatility in the design and assembly process. Our silicones reliably seal, bond, coat, gasket, and encapsulate to protect sensitive components and modules, increase the reliability, and extend the useful life of your product.
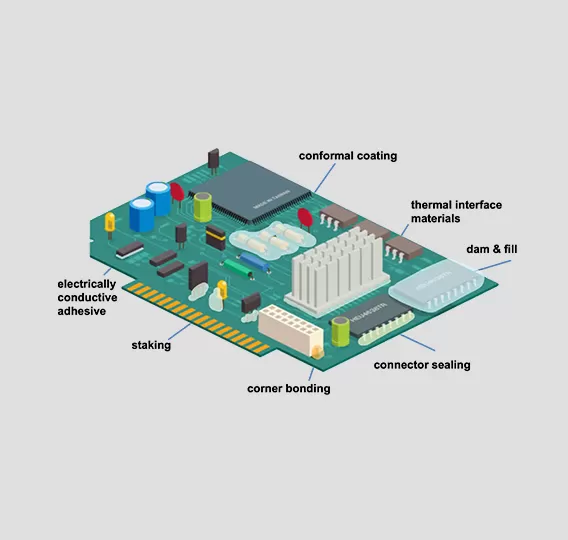
Why use alkoxy silicones in electronics?
- Non-corrosive
- Flexible and durable
- Environmental, UV, and chemical resistant
- Excellent physical properties
- Superior dielectric performance
- Primerless adhesion
- Thermal stability
- Preferred solution for shock absorption and vibration damping
- Easy to dispense
-
UV Cure and UV/Dual Cure Silicones
800-401 is a UV-only, fast-curing paste with adhesion to many plastics. With nominal viscosity of 300,000 cPs, 800-401 consistently holds its shape even when dispensed into complex shapes.
800-754 is a UV-cure only pottant that cures to a soft, compliant elastomer that relieves stress and strain on delicate components. 800-754 will UV-cure to a depth of 14mm in a single pass.
800-755 is an incredibly soft non-corrosive, single-component gel and is an ideal pottant or encapsulant that will also dramatically increase your throughput.
800-260 is a first-generation conformal coating for printed circuit boards. While its oxime secondary moisture cure provides improved physical properties, it offers limited adhesion and can present potential corrosion issues in enclosed applications. This silicone is rated UL 746 E and V-1.
With viscosity of 50,000 cPs, 800-750 clings readily to components for staking and glob-top applications.
800-230 is a UV curable self-leveling silicone pottant that offers a higher viscosity coating option, while still remaining flowable.
800-235 is UV-cured, semi-flowable material. A UV-cure only silicone with limited adhesion, its higher viscosity makes it ideal for cured-in-place gaskets.
800-400 is a UV-only, fast-curing paste without adhesion. With nominal viscosity of ~300,000 cPs 800-400 consistently holds its shape even when dispensed into complex shapes.
800-610 is a low viscosity, pourable or sprayable encapsulant. Its low viscosity ensures the material flows easily around components for thorough wet-out. This is a UV cure with no secondary moisture cure, offering very low adhesion.
800-520FC is a UV-curable, silicone conformal coating, pottant, or sealant. 800-520FC will cure to a solid elastomer in seconds upon exposure to ultraviolet (UV) light.
800-550 is a UV-curable, silicone coating, pottant, or sealant. With a viscosity of 5,500 cPs, 800-550 flows readily to surround the complex geometry of modern circuitry design.
800-505FC is a UV-curable, silicone conformal coating with a secondary, neutral alkoxy moisture cure for enhanced adhesion and shadow cure. It is UL 746E certified with a V-1 rating for flammability. Utilizing our Fast Cure technology, this secondary moisture cure begins immediately and develops full adhesion in hours.
-
Electronics Grade (Alkoxy) Silicones
500-210 is a balanced-performance clear sprayable silicone coating featuring a room temperature alkoxy moisture cure that can be accelerated with heat. This silicone is UL 746E certified and has a V-1 rating for flammability.
500-228 cures to a tough, strong, resilient gel to provide protection from both physical damage and mechanical stress and strain relief in addition to great dielectric properties.
500-09x is a high performance UL-rated electronics adhesive. This one-part UL flame rated paste is for applications that require superior bond strength and flame resistance.
-
Addition Cure Silicones
600-HV is a UL 94 V-0 rated, dual component, platinum catalyzed, addition cure potting encapsulant that forms a durable, flexible elastomer with extremely low volatile content to protect electronic components.
600-223 is a platinum catalyzed, addition cure, dielectric potting gel. This is a specialized silicone encapsulant, with low viscosity for easy flowability around complex components.
600-251 is a platinum catalyzed, room temperature, addition cure silicone for potting and encapsulant applications requiring thermal conductivity.
600-250 is a flowable, platinum catalyzed, addition cure, durable encapsulant with good dielectric properties and flame resistance. The high (>90%) transparency of 600-250 allows for easy inspection of components.
-
High Temperature Foams
60-HTA is a soft, high temperature closed cell foam designed for applications requiring a low force to compress, and for filling large voids and variable gaps.
100-HTA is a high temperature closed cell foam designed for applications requiring both flexibility and strength, and balances compressibility with increase strength and wear resistance.
150-HTA is a high temperature closed cell foam designed for applications requiring a cushion against heavy loads, and withstands wear and abrasion in “tough duty” applications.
-
Thermally Conductive Compounds
G641 offers excellent heat transfer in large and small electrical and electronic components and is an ideal material for use in thermocouple wells, power diodes, transistors, semiconductors, and ballasts. G641, or G644 can be used as direct alternatives to Dow Corning / DuPont Molykote DC340.
Versilube G644 is a softer, lower viscosity version of the original Novagard thermal compound, G641. Both G644 and G641 can be used as direct alternatives to Dow Corning / DuPont Molykote DC340.