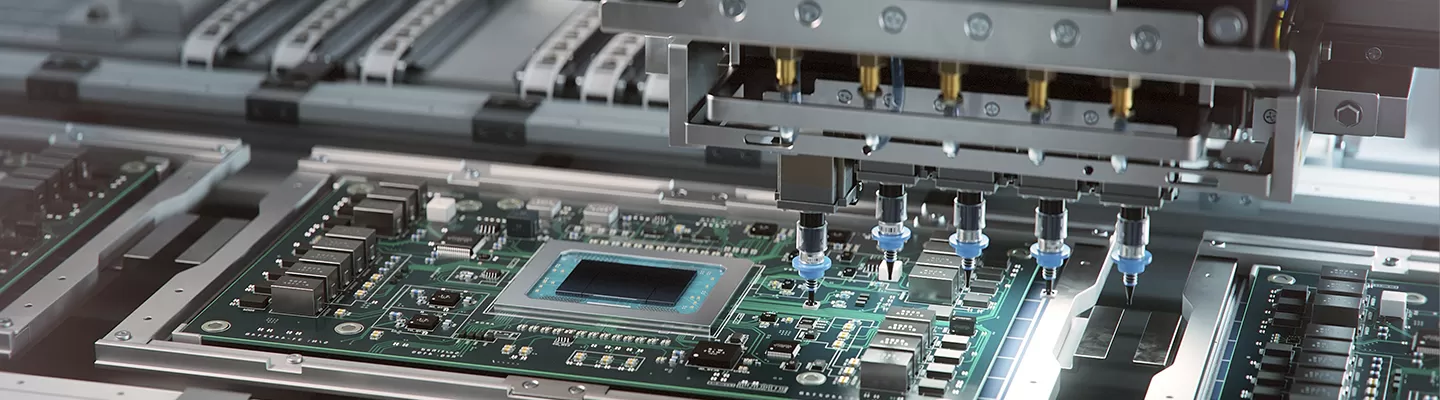
A Guide to the Many Forms of UV Silicones
A Guide to the Many Forms of UV Silicones
As the demand for increasingly sophisticated electronics grows, so too does the need for silicones to take on flow characteristics that can be tailored to specific applications in the manufacturing process.
When it comes to choosing a sealant, the sensitive components of electronics applications have very specific operational goals. Will fine wires or dense components be endangered by thermal cycling? Will the component be exposed to moisture or dust? Is a printed circuit board meant to withstand intense vibration or impact? Whatever the variables, silicone’s modifiable characteristics make it the ideal material for the job.
As electronics continue to be embedded into our daily lives, the need for UV cure silicone sealant products is growing exponentially. Manufacturers are embracing solutions that allow them to cut processing time and cost while delivering world class protection of critical components. UV silicone coatings act as dielectric insulation – a barrier against environmental contaminants such as moisture, dirt, dust, and humidity. They offer a protective layer against abrasions and solvents, and dampen stress causing vibrations of critical components.
To seal and protect sensitive, miniaturized electronics applications, UV cured conformal coatings have become a preferred solution. As the demand for them grows, however, so too does the need for silicones to take on flow characteristics that can be tailored to specific applications.
Enter the broad range of viscosities available commercially today from Novagard, ranging from 500 cPs – 500,000 cPs. We manufacture formulations in the widest range of viscosities that work with every major equipment manufacturer. This includes sprayables for thin section coating, flowables for encapsulation or dam and fill, self-leveling for potting, and pastes for enclosure bonding or staking.
Sprayables
The lower the viscosity (as measured in centipoises or cPs), the easier it is to spray silicone. At 500 cPs to 1,500 cPs, this class of product is primarily used for thin section conformal coating of circuit boards, electronic components, and devices.
Flowables
At 1,500 cPs to 40,000 cPs, flowables are used for encapsulation, or dam and fill. Dam and fill is a two-step process for fully encapsulating a component or section of the substrate. A dam is first created by outlining the perimeter, and then additional silicone material is dispensed to fill its center.
Semi-flowables/self-leveling
These formulations, which are especially ideal for potting, range from 40,000 cPs to 100,000 cPs. Potting encases an entire PCB to protect it from environmental contaminants, and thermal or physical shock. Semi-flowables can also be used for staking, or adhering, a component to a circuit board.
Pastes
For enclosure staking or bonding, and instant formed-in-place gasketing, a great choice are thixotropic pastes, which dispense like a liquid yet hold shape like a paste until cured. They can also be used to create the dam in the first step of a dam and fill encapsulation process.
Whatever viscosity is most suitable, there are added bonuses in terms of sustainability and total cost of ownership. UV silicones are 100% solids, with no VOCs to handle or report. Little or no heat is generated during the curing process so parts remain cool, and can continue to be processed or packaged without racking, limiting work in progress. Win-win-win.